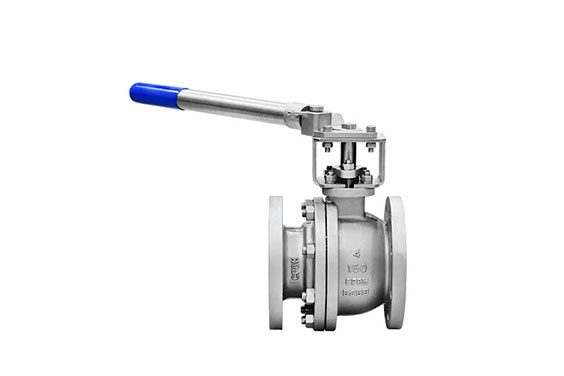
Mechanical devices called actuators to transform energy into motion. Here, a control command causes a physical system to shift, yielding force to complete the task at hand. It is possible to operate the commanding signal manually or automatically, depending on the energy supply.
Actuators regulate machinery and permit the movement of parts, including lifting, fastening, obstructing, and ejecting. Actuators are normally essential components in industrial and manufacturing processes where they turn on valves, switches, pumps, and motors. Dombor valve models are manufactured with durable materials and ensure the highest quality control. This guide will help people learn about hydraulic actuator vs electric actuator.
What Is Hydraulic Actuator
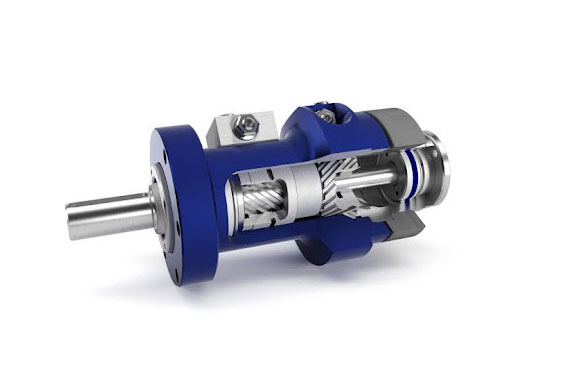
Using a hydraulic actuator, it is possible to convert the liquid’s pressure energy into mechanical energy. The hydraulic actuator consists of a cylinder or a fluid motor that utilizes hydraulic energy to operate mechanically. A rotational, linear, or oscillatory motion is produced as a result of mechanical motion.
The downward chamber of the actuator is attached to the hydraulic supply and return line, which permits hydraulic liquid to flow into and out of the downward chamber. The piston’s action is transferred by the stem to the hydraulic actuated valve. The valve is held in the closed position by the spring force when there is no hydraulic liquid pressure. Pressure in the downward chamber rises when fluid is introduced.
The force produced by this pressure on the piston’s bottom is the opposite of the force stimulated by the spring. The piston starts to move upward when the hydraulic force exceeds the spring force. The spring will be compressed, and the valve will begin to open. Hydraulic oil draining from the cylinder causes the hydraulic force to drop below the spring force, which causes the piston to descend and the valve to close.
What Is Electric Actuator
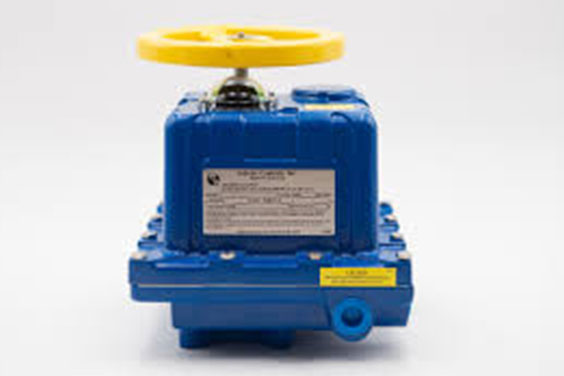
An electric actuator is a machine that may cause movement of a load or an activity requiring a force like fastening, utilizing an electric motor to develop the critical force. As the spindle or rotor turns, the electric motor will produce rotary motion. The motor spindle is connected to a coiled screw through the drive shaft, and it revolves in a ball screw nut.
The ball screw nut is pushed ahead or backside along the helical screw as the spindle turns. As the motor turns clockwise or counterclockwise, a hollow piston rod connected to the ball screw nut generates linear motion out of or into the linear electric actuated valve. The motor’s electric drive regulates the rotation speed, allowing for flexibility.
The linear actuator can be programmed to shift to a specific location, halt, and then continue moving or return to its rest state. The feedback system provides positional data. The torque that can be produced and the force that can be put to work through the actuator depends on the motor’s power.
Hydraulic Actuator Vs. Electric Actuator: Differences
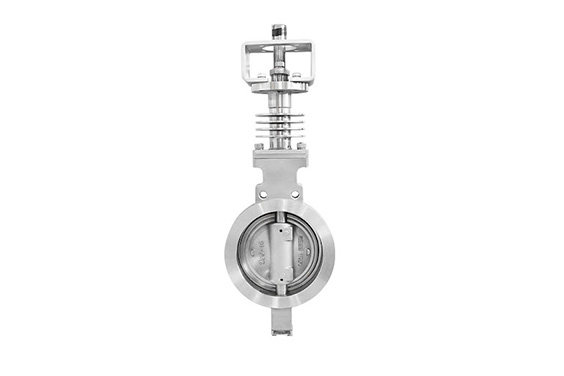
This section will help people understand the differences between a hydraulic vs electric actuator.
Components
Hydraulic actuators retain several various components when it comes to their internal construction. The parts include a hydraulic seal, a stem, a barrel, a stem connector, a piston, a spring, and an inlet and outlet port.
The different components of an electric actuator are front or rear clevis, inner tube, outer tube, spindle component, wiper sealing component, drive nut, limit switches, safety stop, gears, motor housing, dc motor, and output or feedback sensors.
Types
Here is another difference between electric actuators vs hydraulic actuators regarding their types.
- Hydraulic Actuator
Check out the different types of hydraulic actuators:
- Single Acting Hydraulic Cylinder
The hydraulic pressure’s action drives the linear movement in a single direction. When the hydraulic pressure stops, the return movement can be mechanically accomplished by an internal spring that is replaced with the outward mechanical force.
- Double Acting Hydraulic Cylinder
Hydraulic pressure is used by double-acting hydraulic cylinders, which are linear actuators, to move in both directions. In double-acting hydraulic valve cylinders, the piston stroke is significantly longer than in single-acting cylinders.
- Rotary Hydraulic Actuators
Based on the procedure to be performed, whether it is continuous rotation or rotation by a predetermined number of degrees, the hydraulic actuators can be of several types to make a tiny turn of some degrees or 360 degrees rotary.
- Electric Actuator
Here are different types of electric actuators:
- Rotary Electric Cut-Off Actuator
The integrated standard signal is supported by these kinds of actuators. To mechanically operate the valve and complete the automatic modification operation, they transform the signals into comparable angular displacements.
- Linear Electric Cut-Off Actuator
There are two different power supply models for this kind of electric actuator, including AC single-phase and AC three-phase power supplies. The most recent electric actuator is established from the regulator control signal in order to achieve a predetermined linear reciprocating motion.
- Smart Linear Electric Actuator
It is a smart linear actuator with linear output displacement. This actuator is made of high-quality, reliable precision substances and is safe and secure. It has a wide range of applications and is comparable to all types of ball valves, including butterfly valves and control valves.
- Rotary Electric Regulating Type Actuator
This type of completely electronic actuator can work with one grade AC power supply of 220V. It receives input signals of 4mA to 20mA or 1V to 5V dc from the operator, system, or regulator. It is also accessible with a servo system, and additional servo amplifiers are not required. The controller of the input component accepts heterogeneous and sophisticated integrated circuits, and it is subject to aging conduct after being hardened by resin pouring.
- SMC Electric Actuator
These electric actuators have a number of benefits, including regulated and predictable acceleration and speed. Multiple positions can be attained with high precision and reproducibility. Forces are sometimes nearly automatic. There are little to no infrastructural requirements and energy costs when condensed air is not necessary. These actuator types were created with simplicity of use and setup in mind.
Providing Control
When it comes to electric vs hydraulic actuators, the hydraulic actuator performs well in straightforward end-to-end position applications. Complex motion profiles would necessitate pricier servo-hydraulic systems. An electric actuator that has a servo motor allows for limitless variable control over position, velocity, output force, and other factors. It is feasible to change things as you go. The precision levels and repeatability are relatively better compared to the hydraulic system.
Operating Temperature
Hydraulic actuator systems are relatively susceptible to temperature. The oil becomes heavier and moves more unhurriedly in the cold, resulting in a lethargic and uneven performance. High temperatures caused by overheating or the environment may cause the oil to deteriorate or the seals to fail. An additional tank heater is utilized to maintain the operating temperature in the cold, and a heat exchanger controls overheating.
The installation of either piece of equipment raises the costs of the system. As they may be set to operate at a specific temperature for the specified amount of effort necessary, electric actuation systems are less susceptible to temperature. Electric actuators can be provided with severe temperature grease for quick reaction in cold applications.
Footprint
A hydraulic cylinder’s footprint is small where it is utilized, but the hydraulic power unit, which controls oil pressure and flow, requires a lot of floor area. In addition, it may be necessary to include other parts like gauges, heat exchangers, accumulators, and wires. With its mixture of actuator, cords, drive, motor, and cabinet, an electric actuator has a relatively compact total footprint. Simply a speck of the area needed for the hydraulic cylinder with HPU is accepted in the electric servo mechanism.
Hydraulic and Electric Velocity
High-force delivery can be challenging for both hydraulic and electric actuators. For a hydraulic cylinder, there must be enough pressurized fluid in the system to pump the fluid into the cylinder in the appropriate amount of duration in order to accomplish fast speeds at greater forces. There might be a requirement for an expansion system to maintain the pressurized volume.
For a high force to be produced, an electric actuation system depends on the motor’s RPM, torque, and screw properties. However, the speed is limited by the drop in RPM that happens as the torque rises as the servo gets bigger.
Positively, since it has supervision over the complete motion profile, the electric actuator need not fondle the full length of every cycle. As the actuator can make quicker, more competent movements, it might be able to produce peak velocities. It is best to get the valves that are made with quality control measures.
Lifespan And Maintenance
If adequately retained, hydraulic cylinders are tough machines that offer lengthy service life. However, maintenance necessitates team time, the downtime of the machine, and fresh seals, lubricants, and filters. There will be no downtime since there will be no need for maintenance if the electric linear actuator is sized correctly for the application. Beginning with a precise calculation of actuator life, the choice of an appropriate electric rod can be made.
How To Choose Hydraulic Actuators and Electric Actuators
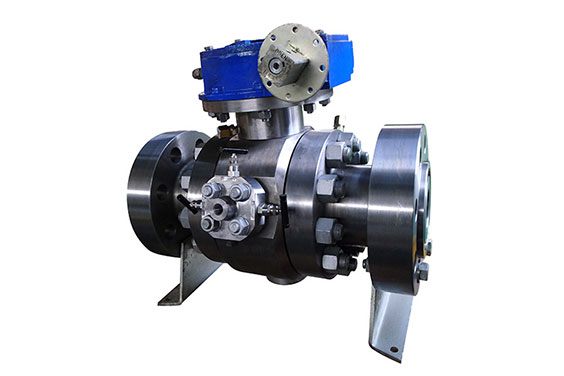
Each actuator produces motion in some way from stored energy, but how well they can manage that energy and transform it into work differs. Knowing the specifications of the actuator’s working environment and the expectations can help one determine which actuator is suitable for the chosen application. Both actuators serve a wide range of applications in various industries.
Choose Hydraulic Actuators:
Here are the applications of hydraulic actuators:
- They are utilized in elevated force-based applications.
- These actuators are employed for different applications such as crane drives, self-driven cranes, winches, excavators, wheel motors in martial automobiles, agitator drives, feeder drives, etc.
- They are primarily used in roll mills, trammels, kilns, mixers, drum drives, shredders for automobiles, tires, drilling rigs, lawn trimmers, trench cutters, etc.
- It may be utilized as a sensor.
- Regulating close-loop velocity
- Very accurate positioning for massive loads
- Hydraulic brake
- Hydraulic jack
- Hydraulic ram
Choose Hydraulic Actuators:
Electric actuators are present in a broad range of industrial applications, which are as follows:
- These are found in the automotive sector for driverless vehicles, dispensing, and choosing of combining procedures such as gluing, fusing, and riveting.
- Manufacturing of PET bottles, packing and labeling equipment, and robotic applications like milking robots are all applications in the food and beverage business.
- They are extensively utilized in the packaging industry and in material handling for tasks like servo presses and clamping.
- Their application in electronics, robotics, electronic assembly, machine tools, as well as many other industrial areas, is made possible by their precision, flexibility, and cheap operating expenses.
Conclusion
The industrial working environment will determine whether an electric actuator or a hydraulic actuator is ideal for the desired applications. In clean rooms, electric actuators are the sole practical alternative. In heavy-duty outdoor environments, hydraulic actuators are pretty common. The power that each actuator can manage makes up the majority of their differences.
Whether looking to order hydraulic actuated valves or electric actuated valves in bulk quantity, reaching out to a reliable valve manufacturer is the best choice. So, contact Dombor to acquire valves for your business needs at affordable rates.