Ball valves come under the quarter-turn valve group and can create a 90 degrees direction, which enables or halts the media flow via a ball-like tool present inside the valves. For industrial applications, they ensure a strong shut-off seal and are simple to use.
Chemical factories, mines, and non-refinery environments frequently employ industrial metal-seated ball valves. These valves manufactured by certificated industrial valve manufacturers are used in procedures that call for essential isolation, high pressures, high temperatures, erosion, corrosion, and abrasion. Go through this guide to get to know more about orbit rising stem ball valve models.
What Is An Orbit Ball Valve
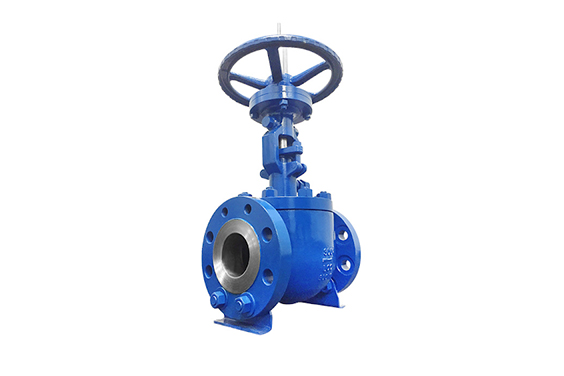
Orbit valve is one common type of ball valve. Seal rubbing is prevented by the tilt and turn mechanism used by orbit valves. In ball valves, gate valves, and plug valves, seal rubbing is the primary reason for failure. These valves have sturdy seals that are primarily built of metal to improve their capacity to function in demanding and hostile environments.
Flow lines, dryer switching, emergency shutdown, bypass and block, product segregation, suction isolation, and discharge are just a few applications where orbit valves are appropriate. Orbit valves are employed by a number of industries, including the petrochemical, gas, and oil sectors.
In order to assist prevent seal rubbing, which is the primary source of wear in ball valves, orbit valves are constructed with switch and tilt operation. The orbit valve core immediately jams up against the seat when the valve is closed. The valve improves positive shut-off when it is in this posture.
The core is tilted far from its seat when the valve begins to open, enabling line flow to circulate equally around the core face. In conventional ball valves, localized high-velocity fluid flow leads to irregular wear on the seat, and it helps to eliminate that. The core then rotates to finish in an open state.
Without the seal scraping through every closing and opening, low torque, valve operation, and long-term dependable valve performance are improved. Switching the handwheel begins lessening the stem when the orbit valve is closed. Precision grooves in the stem work against stabilized guide pins to cause rotation of the core and stem.
The stem and core can spin to accomplish a 90 degrees revolution without the core touching the seat as you keep swerving the handwheel. The wheel’s final turn mechanically forces the stem downward. It aids in stopping fluid flow by forcing the core firmly against the seat.
Explaining The Operating Principle of Orbit Ball Valves
Each orbit ball valve features a tried-and-true tilt and turn mechanism that gets rid of seal rubbing, which is the main reason why valves fail. A positive shut-off is ensured when an orbit valve is closed by the core being mechanically jammed firmly against the seat.
The core leans away from the seat as the orbit valve opens, and line flow spreads evenly across the core face. This stops the rough seat wear that often occurs in the regular ball, gate, and plug valves due to localized high-velocity flow. After that, the core turns to its fully open state.
Seal rubbing is prevented during both valve opening and shutting, resulting in simple, less-torque valve function and long-term dependable performance. The orbit performing concept may be trusted to produce a positive shut-off when valve leaking cannot be tolerated.
The stem lowers as the handwheel is rotated to close an orbit ball valve. The stem and core will spin as a result of how precisely the cut spiral grooves in the stem interact with fixed guide pins. The core and stem spin fully 90 degrees when the handwheel is turned continuously without the core getting in contact with the seat. The stem is mechanically wedged down and the cure is securely pressed onto the seat by the handwheel’s last spins.
Orbit Ball Valve Product Range and Options
The orbit ball valves are produced in different types of sizes, materials, sizes, and trims in order to fulfill the requirements of various applications.
- Materials
Depending on the needs of the service, carbon steel, duplex stainless steel, stainless steel, high nickel alloys, and various specific substances are employed. For increased longevity in corrosive environments, protective layers on both the inside and exterior are provided.
- Seats
For the desired service, soft or metal seating alternatives are chosen. The valves survive in hot, abrasive environments as their seals do not stroke together and they are mechanically squeezed closed.
- Operation
You can choose between power and hand operation. Orbit valves create pneumatic actuators that are double acting, spring close, and spring open. Both electric and hydraulic actuators can be chosen. There are numerous instrumentation options available.
- Customization Options
The customization options include warm jackets, handwheel extensions, security interlocks, position indicator limit switches, custom painting, and special inspection.
Features Of Orbit Ball Valve
Here are the standard features of the reliable orbit valve you can find on the market.
No scraping Between sealing surfaces
In conventional ball valves, gate valves, and plug valves, seat wear is mostly brought on by seal abrasion, which is eradicated by the tilt-and-turn movement.
Individual Seat Design
The orbit valve eliminates the issues associated with trapped pressure between labels by using an individual, fixed seat that seals in double directions.
Maximal Flow
High CV numbers are produced by full port or reduced port apertures. Both erosion issues and system pumping efficiency are improved.
Extended Lifespan
The long-lasting orbit valves can replace other problematic gate valves, plug valves, and globe valves. The orbit valve architecture delivers performance benefits that lower maintenance costs and plant outages.
Injectable Packing
In order to completely regulate fugitive emissions during in-service care and maintenance, stem stuffing substance is pumped through the packing fitting.
Top-entry Structure
The top-entry structure facilitates maintenance by allowing in-line examination and repair after system depressurization.
Self Simple Cleaning
Before rotating, bending the body away from the seat causes an abrupt flow of 360 degrees around the core exterior. Without relying on a single, concentrated area of high-velocity erosive flow, the product flow washes out any new material away from the seat.
Two Stem Guides
The lift-and-turn motion of the stem is regulated by strong guide pins and solidified stem openings.
Low-torque Performance
As the seal rubbing is removed, it allows for easy valve rotation of the orbit valves.
Automatic Cam Closure
A mechanically powered seal is provided by the cam angle at the stem’s deeper end.
Wear-resistant Core Hard Facing
The core face is made of a tough, polished substance that can withstand demanding use without losing its sealing integrity. In addition, it shows resistance to wear.
Types Of Orbit Ball Valve
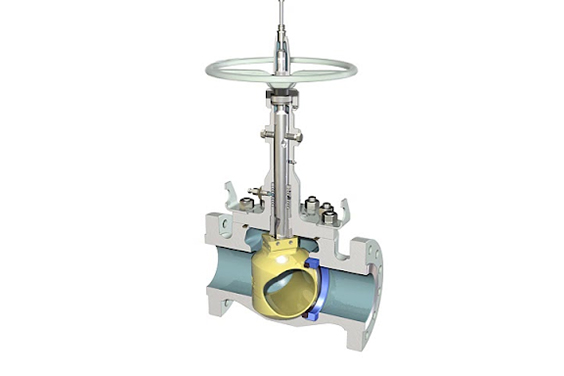
Here are the primary types of orbit valves that everyone should be aware of:
Manual orbit ball valves
A manual actuator is used to regulate fluid flow in manual orbit valve models. These valves utilize a handwheel mechanism to improve flow control instead of requiring external power. A number of gears in the valve’s mechanism increase production torque in relation to the input torque that the valve operator applies.
The advantage of manual orbit valves is that they are affordable, dependable, and independent of outer power sources such as pneumatics and electricity. Since these valves are self-contained and utilize the exact handwheel to unlock and shut down, it is simple for the operator to identify the root of any technical issues or mistakes.
However, because it is not possible to automate the manual orbit valves, they must always be operated manually. It would imply that a valve operator would need to be present in order to monitor and control the valve’s proper operation.
Hydraulic orbit ball valves
Fluid under pressure is utilized by hydraulic orbit valves to regulate the flow of the liquid. These valves employ oil or water as the hydraulic liquid. The piston rolls as a result of the fluid’s pressure, regulating the fluid flow. Hydraulic orbit valves come in semi-automatic and automated varieties.
In comparison to pneumatic orbit valves of the exact size, the hydraulic orbit valves tend to be more robust. Due to the incompressibility of the liquid, these valves can accomplish fine fluid control with low energy loss. However, to improve liquid flow, hydraulic orbit valves require an extra hydraulic pipe. Additionally, these valves might leak hydraulic liquid, which increases the chance of a high fire risk.
Pneumatic orbit ball valves
Pneumatic orbit valves are those that are operated by compressed air. These valves operate by applying air pressure to the piston or diaphragm that is fastened to the valve stem. Pneumatic orbit valves, in contrast to manual orbit valves, can be fully or partially automated.
Because of the subtle design and dependability, the pneumatic orbit valves are the most popular form of orbit valve. The benefits of pneumatic orbit valves are little to no fire hazards, simple and dependable design, manageable operation, and inexpensive prices. But, these valves might not work well at slow speeds.
Electric orbit ball valves
Valves that rely on electricity to function are known as electric orbit valves. Electric motors are utilized in these valves to transform electrical energy into mechanical energy sufficient for unlocking and shutting down the valve. As they can be opened and closed manually, automatically, or semi-automatically, the electric orbit valves are highly flexible.
The motor in electric orbit valves can move both ways, and it aids in gearing up the valve stem. Electric orbit valves have the benefit of not requiring liquid or pressurized air and being able to provide extremely high torque for heavy-duty uses. However, in comparison to manual and pneumatic orbit valves, these valves are highly costly. In addition to that, the electric orbit valves are also prone to power outages and fire hazards.
Orbit Ball Valve Parts
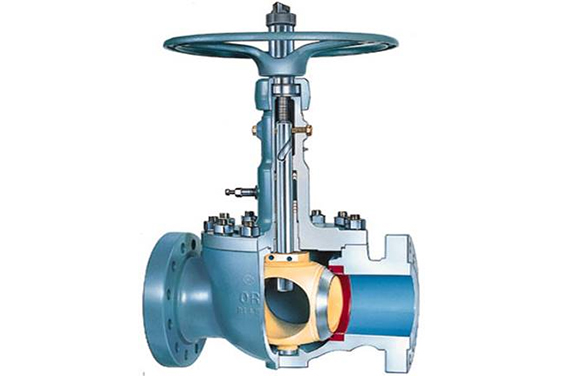
Orbit valve has several components, and the major ones are listed here.
- Stem
The stem is a sturdy part prepared of steel or other metallic elements. It is utilized to link the valve’s internal mechanism to its outer control mechanism. In a nutshell, the stem links the actuator and orbit valve.
- Valve body
An orbit valve’s external casing is known as the valve body, and it serves to store the orbit valve’s interior parts. For the valve body to survive the tremendous pressures brought on by the flowing liquid, it must be sturdy. Due to that, the valve body is made of materials like carbon steel, brass, and stainless steel.
- Bonnet
The part of an orbit valve that covers the valve body is the bonnet. This component is fastened to the valve body either with screws or nuts and bolts. When launching an orbit valve, the interior parts are first put into the valve body, and after that, the body and bonnet are linked.
- Actuator
An orbit valve’s actuator provides the necessary power to open and close the valve. It could be a hydraulic, electrical, pneumatic, or mechanical actuator.
- Bearings
Bearings are utilized to increase low operating torque, decrease wear, and sustain the orbit valve’s shaft against stresses. In order to endure the internal pressure and weight of the elements, bearings are built of sturdy materials like stainless steel.
- Anti-fire gasket
This gasket is utilized for safeguarding the valve from fire, particularly when it is working with flammable materials like petroleum. Graphite and other anti-fire substances are used to make the gaskets.
Orbit Valve Diaphragm
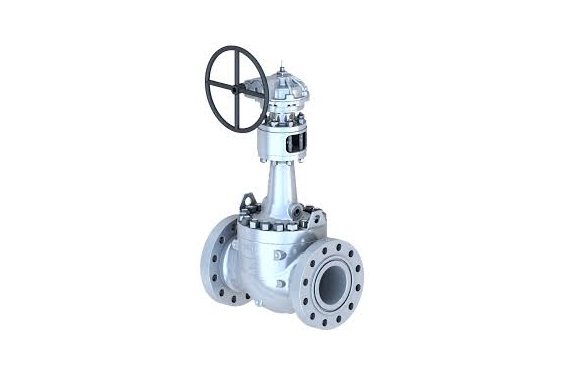
A diaphragm valve is a type of valve that controls liquid flow using an adaptable diaphragm. The membrane valve is another name for the diaphragm valve. The flexible membrane or diaphragm responds to pressure, and this component applies force to control, close, or unlock the valve.
A “pinching” technique is used by a diaphragm valve to control liquid flow through the valve. A compressor is connected to the diaphragm, and the stem is further attached to this compressor. The valve operator raises the stem to boost fluid flow when needed. The compressor is further raised as a result of the stem’s upward movement. The attached diaphragm receives more motion from the compressor, and it begins to rise as well.
As per the needs of the operator, the liquid flow rises as the diaphragm surges. The operator rotates the stem and shifts it downward to reduce or shut down the liquid flow. The compressor receives the motion from this stem and transmits it to the diaphragm, compressing it further under and lessening or locking the flow.
Additionally, a few valves can throttle liquid flows. The diaphragm is therefore somewhat closed and somewhat opened. The diaphragm valve has the following major components: stem, compressor, bonnet, and actuator.
Pros And Cons Of Orbit Ball Valve
The orbit ball valves are suitable for a variety of applications, including mol sieve dehydration switches valves, dryer switching, meter isolation, flowlines, product segregation, heat transfer fluids/hot oil, emergency shutdown, hydrogen service, block and bypass, suction and discharge isolation, and so on.
Have a look at the primary advantages and disadvantages of orbit ball valves.
Pros of orbit ball valves:
- Orbit ball valves have a straightforward design that makes repairs simple.
- Seat rubbing is absent from orbit valves.
- Orbit ball valves show high resistance to corrosion.
- Since these valves do not leak, there is less waste and environmental degradation.
- Orbit valves are abrasion-resistant.
- The orbit valves have a top-entry design that makes it easier to access them for repairs and in-line examination.
- In order to transfer hot or heat transfer liquids, these valves can be utilized.
- These valves can be applied during a shutdown emergency.
- Depending on the priorities of the client, several actuators can be used to operate orbit valves.
- The operating temperatures for these valves vary from -104 degrees Celsius to 427 degrees Celsius.
- The orbit valves have a self-cleaning feature.
Cons of orbit ball valves:
- In comparison to other valves, orbit ball valves are relatively pricey.
- Orbit ball valves are employed in sensitive applications where proper operation is required to prevent creating irreparable environmental damage, such as those used in the petroleum sector.
What Factors To Take Into Account When Acquiring Orbit Ball Valves?
Here are some factors that one needs to consider while acquiring orbit ball valves for industrial requirements.
- Temperature Range
Orbital valves can function in a variety of pressure ranges. However, the producers of orbit valves provide the valves with a particular operational temperature range. Knowing the media’s lowest and maximum temperatures is crucial before buying the orbit valves. The valve could get harmed by elevated temperatures. On the other hand, it is possible for the valve to freeze at extremely low temperatures.
- Pressure Rating
Manufacturers of orbit valves design their valves with varying strengths to accommodate various pressure levels. As a result, before choosing an orbit valve, consider how much pressure it will be subjected to. Depending on the amount of pressure the media will exert, this can be specified. The orbit valve will be harmed or the valve operator will be hurt if the fluid pressure strength is greater than the strength of the valve.
- Power source for the orbit valve
An orbit valve’s opening and shutting require some power in order to provide a turning effect for shutting down or opening the valve. The actuator to be utilized is determined by the power source. As a result, choose the orbit valve depending on the actuator type that is available: manual (hand-operated), pneumatic, hydraulic, or electrical.
- Size of the valve
It is crucial to know the size of the valve so you can get an orbit valve that will match the other plumping components without difficulty. In addition to that, this will prevent the need to modify the piping system or guarantee that the orbit valve does not collide with other piping system parts.
- Environmental conditions
In this situation, the valve may be disclosed to elements that could impair its functionality, like extreme heat or cold and corrosive media. If the valve is operating with volatile materials like petroleum, a hot environment could harm it or even set it on fire. Freezing can happen at extremely less temperatures. Corrosive substances can weaken the valve body by damaging exterior valve components including screws, nuts, and bolts.
- Weight and assistance
The weight and support of the orbit valve must be taken into account. A few valves are quite hefty, and this may put a lot of strain on other pumping parts, eventually causing them to fail.
What Are Different Orbit Ball Valve Troubleshooting
Check out the below-listed orbit ball valve troubleshooting problems.
1. Structural Breakage
- Handle broken
It may be the result of frozen activities or an outer effect. To fix this, it is vital to specify and rectify the source of the issue.
- Stem broken
This problem might arise because of outer effects or frozen operations. Check frozen movement solution criteria and the cause of the impact failure.
- The end connection is broken.
It may be the result of misalignment or because of exterior impact. Make sure that the system alignment is proper.
2. Body Is Broken
- System misalignment
It is vital to check that the system is correctly aligned.
- Excessive internal pressure
Make sure that the interior pressure is the same as instructed by the orbit valve producer.
- Chemical attack
It is necessary to check if the chemical working on the orbit valve shows compatibility with the interior substances of the valves to deter an attack on the valve.
3. Internal Leakage
- Thermal damage.
It has the potential to distort the orbit valve. Inspect the orbit valve functioning temperature range along with exterior heat sources generated from the system design.
4. Difficult In Closing Or Opening The Valve
- Internal obstacle or sediment accumulation
Peel off the orbit valve to inspect for garbage, solids, or sediment deposits. Make sure to tidy up these substances and reinstall the valve once more.
5. Orbit Valve Not Shutting-off
- Mistaken direction of rotation
Inspect the closing of the valve’s direction as per the guidelines and instructions of the manufacturer.
- Faulty automation
For automated orbit valves, the problem may arise because of faulty actuators. In the case of a semi-automatic valve, it is best to utilize a manual system to close down the valve.
Conclusion
Orbit ball valves are utilized all over the world in vital isolation applications because they are suitable for applications that demand no leakage and systematic operation. With their tilt-and-turn function, these valves deter seal rubbing, which is the main reason for valve failure. Seal rubbing is prevented during both valve opening and shutting, resulting in simple, low-torque valve operation and consistently dependable performance over time.
When purchasing orbit ball valves, it is vital to consider a few factors, such as temperature range, pressure rating, total weight and support, the power source for the orbit ball valve, and environmental conditions. Make sure to get in touch with a trustworthy industrial ball valve manufacturer to acquire suitable orbit ball valves in bulk for your business requirements.