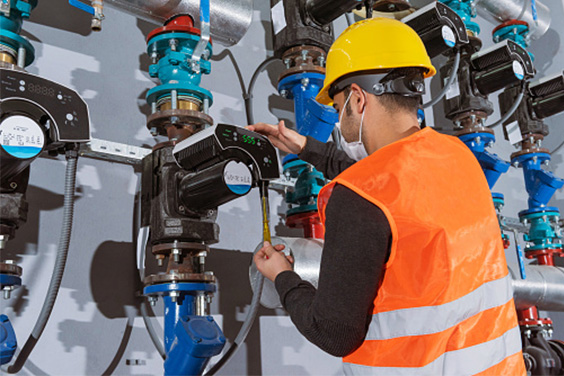
Industrial Globe Valves control the flow of liquid or gas into a process or through a pipe. They’re an excellent choice for this task because they seal tightly when closed but are easy to open with minimal effort. They are commonly used in chemical, food, and pharmaceutical processes and heat transfer.
Installing a globe valve isn’t a complex process, but it is required to follow the procedure to avoid potential problems. It is also essential to install the valve correctly to ensure it can function as intended. Operational leakage, pressure loss or the inability of the valve to open or close properly when needed can all be issues caused by improper installation of a globe valve. To help avoid these problems, we’ve put together this industrial globe valve installation guide.
This installation guide details the necessary steps to mount and operate industrial globe valves successfully. It will answer critical questions about their effectiveness and assist in choosing the best process for implementation within the business.
What are Industrial Globe Valves?.
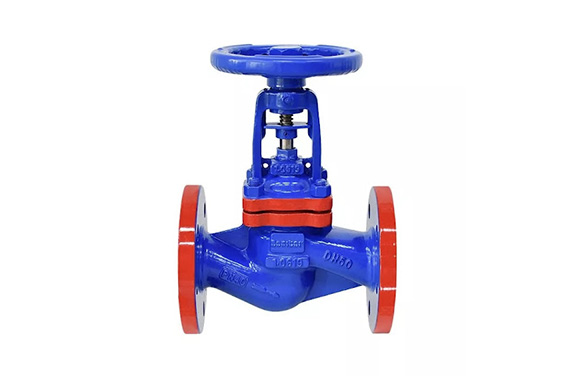
A globe valve is a type of valve used for controlling the flow of liquids and gasses. It consists of a round body with a movable disk-shaped element inside. The disk is connected to a stem used to open or close the valve. Globe valves are typically used in industrial applications where a large fluid flow needs to be controlled.
Industrial Globe Valve, also known as pneumatic globe valves, are valves that have rotatable discs (called “discs” for short) as their movable parts, as opposed to a pivoting “flap” seen in most other valves. The discs on a globe valve can be rotated to seal the flow path or be removed entirely from the flow path. A globe valve can be part of a system and the entire system. When closed, the discs create a seal between the process, which allows the valve to be fully completed and ensures no leakage between the other two points. When the valve is opened, the discs will not be in contact with the surface they were sealing against. This allows the new process to flow into the valve and then out of the valve with zero resistance.
Construction Of A Globe Valve
A globe valve is a type of valve used for regulating flow in a pipeline. It consists of a round body with a movable disk-shaped element that controls the flow of fluid through the valve. Globe valves are often used in applications where a high degree of accuracy is required, such as in controlling water pressure in a pipeline.
The construction of a globe valve is relatively simple. The valve’s body is typically made from cast iron, although other materials such as steel or brass can also be used. The disk-shaped element, the plug, is attached to a stem that runs through the body’s center. The stem is connected to a handwheel on the outside of the body, which is used to open and close the valve. There are several types of Globe valves according to the design and construction:
1. Based on bore pattern
Straight Through/TEE Pattern/Z-Body Globe Valve
The T Pattern Globe’s medium inlet and outlet flow paths are 180 degrees each. This design has a low coefficient for flow and pressure drop. The valve stem guides the valve disc towards its sealing surface. The friction between sealing surfaces is minimal during open/close, which reduces wear and tear. The process performance and throttling height are minimal. It is much simpler to maintain than a gate valve. This valve is the most used in the industry.
Y Type Globe Valve
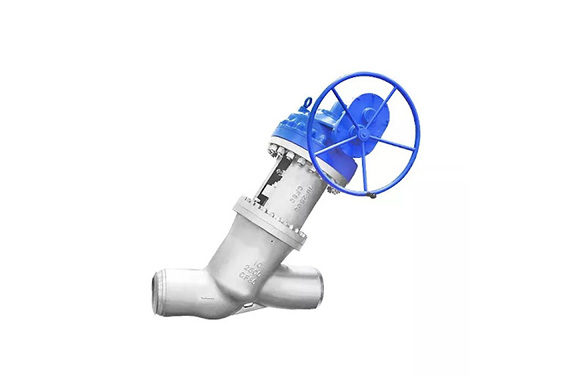
The flow path of the Y-type globe Y valve stem forms an angle. Also, the sealing surface and inlet/outlet flow path have an angle. The body of the valve can be either an integral or split-body. The split body type of the Y globe valve has two valve bodies that sandwich the seat. This makes it easy to maintain. The flow direction of the Y-type globe valve does not change. It has the lowest flow resistance of all globe valves. To resist corrosion and erosion, the sealing surfaces of the valve seat or disc can be welded using a hard alloy. It is ideal for pipelines that use alumina production.
Angle Globe Valve
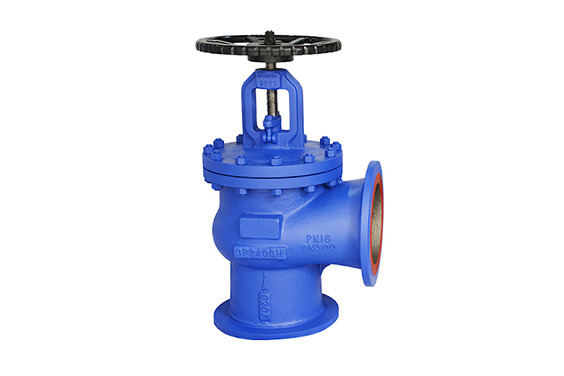
The greatest benefit of the angle globe valve is its ability to be established at the correct angle of the pipeline system. This holds 90deg elbows. It is also easy to use. They are used in various applications, from regulating flow in pipelines to controlling pressure in process systems. Angle globe valves provide reliable service and long-term performance in demanding environments.
2. Other Globe Valve Types
Bellow globe valve
A bellow globe valve is a type of valve that uses bellows to seal the valve. The bellows are also made of a material that is resistant to the pressure that is being applied to them. The bellows are attached to the valve body at the top and bottom. The bellows are also attached to the valve stem. The bellows are inflated when the valve is opened. The bellows are deflated when the valve is closed.
Plunger Globe Valve
This type of plunger valve has a radial seal. It is achieved by two spring-loaded sealing rings that are attached to the polished plunger. The collar separates the seal rings. The load is applied to the bonnet through connecting bolts. This forces the spring-loaded seal around the plunger to seal tightly. The valve materials combine carbon steel for the body, Cr13 stainless for the plunger and flexible graphite to seal the ring. If the body and plunger are made from stainless acid-resistant, with PTFE seal rings, they can be used in acid or alkali corrosive media.
Needle Globe Valve
In needle-type globe valves, the stem and valve disc are often integrated. It is fitted with a needle-shaped probe and matched with a valve seat. The thread pitch of this needle-type globe is also smaller than the general globe’s stem thread. Normal circumstances will mean that the seat hole of the needle globe valve is smaller than the pipe. It is therefore not recommended for use in pipes with small nominal diameters.
Three Way Globe Valve
The three-way globe body can have three flow paths and be made four-way. The three-way valve can replace the existing three-way joint or three other globe valves. High-performance sealing ensures that the three-way globe valve will last longer and is leakproof. It can also reduce maintenance costs.
How Does Glove Valve Work?
A globe valve can be used in unidirectional applications. It can only be installed in one direction. It can be installed in one direction using a disc, handwheel, or stem. The globe valve regulates, starts, and stops the fluid flow. The following is how a globe valve works:
- The valve handwheel is rotated by an operator, which allows the flow to be controlled, closed, or opened.
- The stem is connected to the handwheel, which is then connected to the valve disk.
- The operator turns the handwheel counterclockwise to reduce or close the fluid flow. The handle then transfers its downward motion towards the stem.
- When the stem is subject to handwheel motion, it moves down and pushes downward the valve disc.
- The fluid flow is stopped by the downward motion of the valve disk.
- To open the valve, the operator must turn the handwheel in the opposite direction. Under such conditions, the stem pulls on the valve disc and takes the disc out of the two valve seats.
- The operator controls the handwheel so that the valve disc opens and closes in a manner that throttles flow.
Safety Notes In The Operation Instructions
There are a few safety notes to remember when operating a globe valve.
- Always open or close the globe valve slowly to avoid sudden pressure changes.
- Always wear gloves when handling the valve
- Never use a globe valve to throttle flow.
- Globe valves are not designed for frequent operation.
- Always install a globe valve in a horizontal pipeline.
- Always use a wrench to operate a globe valve.
- Always keep the valve in an upright position to avoid spillage.
Globe Valve Installation Steps
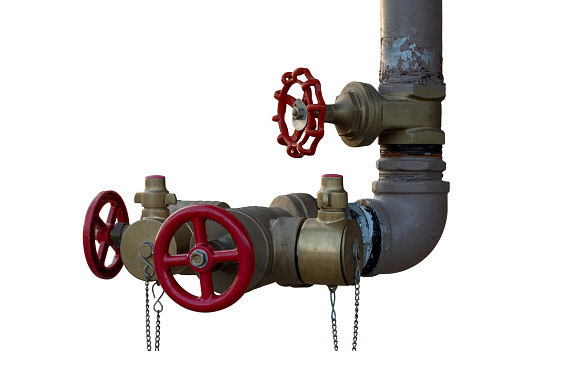
Globe valves can only take flow under the disc because they are unidirectional. The body of the valve has an arrow indicating the direction of flow. However, it is easy to check by looking at one end of the valve. This will allow seeing if the valve is facing the underside or the top of the seat. The handwheel operation should be at the valve top. This will ensure that the valve is not prematurely worn or damaged. These are the main points of the globe valve installation position.
- Take out any packing material or other debris.
- Make sure the innards of the valve are dry.
- Make sure the valve is supported correctly. This can be caused by unsupported long runs clamping into the valve.
- Be sure to have enough space to employ the valve
- Perform a dry cycle to change the valve’s position from closed to open and back again
- In a diagonal pattern, tighten the flange bolts gradually.
- Gradually increase the inner pressure until the bolts and flanges are correctly installed, and the valve seals.
- Increase internal pressure to operating levels, and then check again
These are the basic steps that are required to install an industrial globe valve:
- Unpacking the valve – The first step toward installing an industrial valve is to empty it. This includes reading all instructions and diagrams printed on the valve’s packaging.
- Positioning the valve – Next is to position the valve. This includes finding the best location for the valve and the location for the upstream and downstream connections.
- Pressure testing the valve – Next is the pressure test of the valve. This is important to ensure that the valve is functioning correctly and have to replace the valve if it does not pass the pressure test.
- Mounting the valve – After the successful pressure tested the valve, now it’s time to mount the valve. Ensure the valve is correctly secured in its mounting location.
- Finishing installation – The last step in installing an industrial globe valve is finishing the installation. This includes connecting the valve to the upstream and downstream connections.
- Next steps – Finally, move on to the next steps. This includes starting the process and ensuring that the valve performs as expected.
After Installing a Globe Valve
After installing an industrial globe valve, take a few steps to ensure it’s operating at peak performance. This includes maintenance and operational tips to help in getting the most out of the valve.
Maintenance
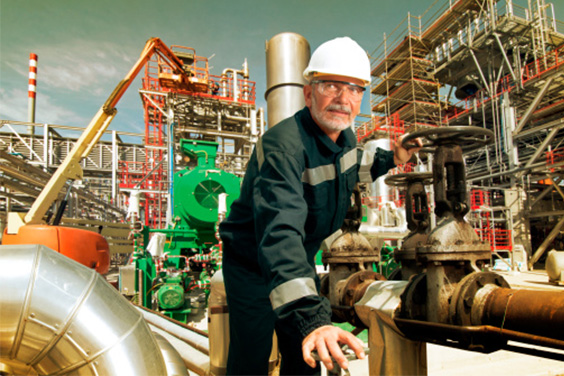
Regular maintenance and inspections will ensure that the globe valve lasts as long as possible. It’s essential to maintain the valve. These are just a few of the things that one should consider. This includes cleaning it regularly and inspecting it for damage or issues. If there is any problem with the valve, make sure to correct the matter as soon as possible.
- Frequent assessment of the valve is recommended. Pay a special lookout to the gland to make sure there is no visible wear or if the valve is dripping.
- It is a good thought for the valve to be cycled if it is not used often. This will ensure that the disc does not become lodged in the seat.
- Use a grease gun as a lubricant on the crossbar using the grease nipple. If necessary, grease the spindle.
- If the packing needs adjustment, tighten the bolts slightly. The gland may be damaged if they over tighten. The gland packing may need to be replaced if it is still leaking.
It is important to note that the valve must be removed from the main line to allow for inspection. This is to ensure there is no water in the pipe and that it must be cooled down to room temperature. After the valve is removed, a thorough inspection needs to be done. This includes an examination of the valve seat and the disc and can remove any scale from the valve’s bottom.
Operation
It’s also essential to operate the valve correctly. This includes following the manufacturer’s instructions and instructions on how to use the specific valve.
- Globe valves open in an anti-clockwise direction and close in a close-wise order. To complete the seat, do not tighten it too much and might have to remove any media still getting through the seat.
- They are excellent for controlling flow, but it is advised not to leave them in the middle for long periods. This can cause premature wear to the seat. In steam applications with continuous throttling of less than 10%, excessive vibration, noise, and wire draw across it may result in a leak path that is not visible to the bare eye.
- During operation, it is recommended not to overreach the highest pressure rating of the valve. Operators are responsible for any pressure spikes or changes that exceed the valve’s maximum pressure rating. If not followed, this can lead to severe harm or damage.
How To Transport Globe Valve After Installation
After installation, globe valves must be transported with great care to avoid damage. Globe valves are delicate and can be easily damaged if not handled properly. Here are some tips on how to transport globe valves:
- Use a soft, padded surface to protect the valve from scratches and other damage.
- Do not use any hard objects to support the valve during transport.
- Be careful not to drop or bump the valve.
- If possible, transport the valve in its original packaging.
- Cover holes with foils or covers to prevent damage to the valve seats.
- The valves should not be hung on the handwheel or any possible motor connected to avoid damage.
- The valves must be checked after delivery and before assembly to avoid any damage during transportation.
How To Storage Globe Valve
The storage must be done in such a way that it continues to work even after extended storage. It is important to keep the valve sealed (to protect the seat faces) and to take precautions against soiling (dust, sand mortar, building materials, etc.), frost, and corrosion with plastic foils. Soft gaskets made of elastomer must be stored in accordance with the following storage guidelines: – Stores should be dry, clean, and well ventilated. The storage temperature should not exceed 25 degrees Celsius. Stocks must be exhausted to avoid prolonged storage. – Valves must be kept in the “closed” position throughout storage. To avoid premature aging of the rubber, the soft closing elements must be closed with very little force.
What Problems Would Occur After Installation Globe Valve
After installation, globe valves can cause several problems. First, they can leak. This is because the seal between the body and the stem is not as tight as other types of valves. Second, they can be difficult to operate. This is because the stem has to be turned to open or close the valve, which can be difficult if the valve is in a hard-to-reach place. Finally, globe valves can rust over time. This is because the metal in the valve is exposed to the elements, which can cause it to break down over time.
If you experience either of these problems, you can take a few troubleshooting steps. First, check if the valve is installed correctly and all the parts are tightened properly. Next, check the seat and disc to see if they are damaged or worn. Finally, check the actuator to see if it is working properly. You may need to replace the valve if all these things check out.
Industrial Globe Valve Selection Considerations
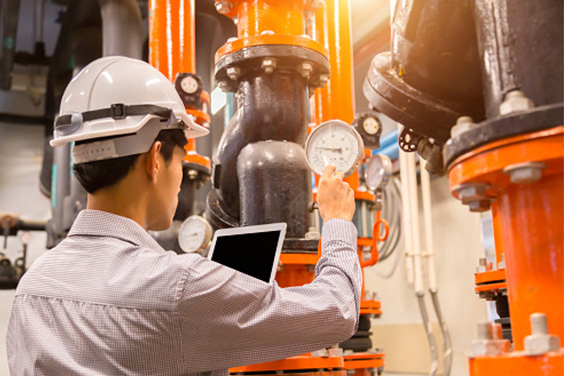
When selecting an Industrial Globe Valve, it’s essential to consider many factors, such as the valve’s application, the materials the valve is made from, and the manufacturer’s reputation.
- Application – The first step in selecting a valve is determining the application. This includes everything from the temperature of the liquid passing through the valve to the pressure the valve will be experiencing. Select a suitable valve for the process whenever possible, but don’t let this be the only deciding factor.
- Materials – Next, need to consider the materials from which the valve is made. This includes the disc materials, the seat materials and the housing materials. If a disc is made from a material that will wear out or corrode quickly, the lifespan of the valve will be decreased. Materials that are appropriately rated will increase the overall lifespan.
- Reputation – The final step in selecting a valve is to look at the industrial valves manufacturers reputation. This includes their track record, handling their customers, and standing behind their products. Companies dedicated to excellence and customer service will more likely provide the expected experience
- Size: The most important consideration when choosing an industrial globe valve is the size and capacity of the process or system. Selecting a valve that’s the right size for application is best. Globe valves come in sizes ranging from 1″ to 2″, corresponding to the internal diameter of the pipes to which the process is connected. It’s also important to consider the size of the equipment on which the process is connected. Choose a larger valve if the application is related to a large equipment volume. However, for a small application, select a smaller valve.
- Pressure Range: Another essential thing to consider is the process’s pressure range. The pressure range of an industrial globe valve assembly is measured in terms of how much the valve opens. Globe valves range from 550-6500 PSI. If the process operates at pressures above these ranges, choose a valve with a higher pressure rating. If the process operates at pressures below these ranges, select a valve with a lower pressure rating.
Bottomline
In conclusion, the globe valve installation guide provides a comprehensive installation process overview. However, it is essential to note that this is only a guide and that professional help should be sought if the installation is completed correctly. Furthermore, the guide should be read entirely before beginning the installation process to ensure that all steps are understood. Also, contact us for more information on installation process or purchasing globe valve