Engine Valves are some critical mechanical components employed in internal combustion systems. Their main task is to enable or restrict the flow of any medium, be it liquid or gas. This flow occurs to and from the cylinders or combustion chambers when the engine gets operated. Talking about the engine valves’ functions, they work the same way as other valves do.
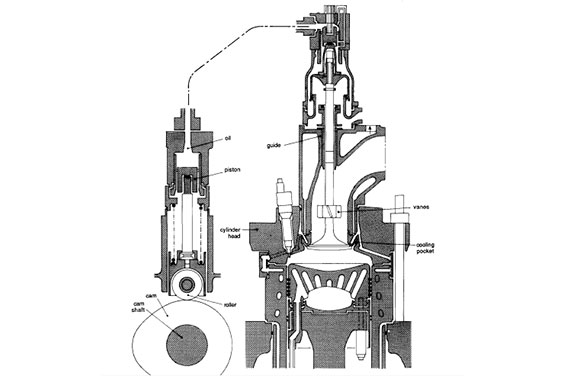
That said, they also work to control the flow. The engine valves are completely mechanical devices that get interfaced with other engine components. One of the instances is the rocker arms to help achieve opening and closing at the correct timing and in the proper sequence.
An engine valve may also be known as a check valve, which is used to inject air as a part of the emission control and the recirculation systems of exhaust gas in vehicles. Today, we discuss the different types of valves used in ships to ensure the best results.
The valve type is used based on the flow pattern and the need for the same. However, all the different kinds of valves used in ship engines share one basic functionality, regulating the liquid flow in a pipe. The valves are employed in almost all machinery systems on a ship since it helps control and regulate the flow of liquid through the pipe. Furthermore, valves are also known as devices that decrease efficiency.
This is because they reduce the energy in the flow of a liquid. Hence, using any valve is imperative for applications requiring limited flows. One of the valves that are highly used in ship engines is the gate valve. Please keep reading to know more about how they are used and what makes them the first choice to be used on board ships.
Common Ship Engine Valves
Ball Valves
The ball valve, like the butterfly valve, is a “quarter turn” valve. They are similar in design in some aspects, being as simple and reliable. Small sized valves have a floating ball between the PTFE seats. The body is constructed of steel, stainless steel, or brass that has been nickel or chrome plated.
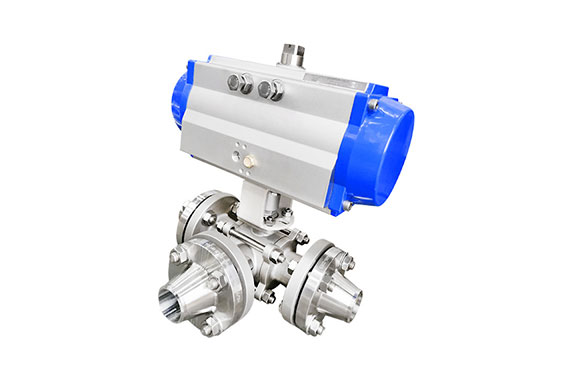
Ball valves can work in a wide range of media at high pressures and temperatures due to their design. Internal line pressure cannot drive out a blown-out stem. However, if you intend to use a PTFE-seated ball valve at high temperatures, always check the maximum working pressure against the manufacturer’s tables.
The straight-through design ensures less pressure loss. Although most types are full bore, reduced bore (bore) ball valves are occasionally utilized for cost savings.
Ball valves are primarily utilized for pressures more than 25 bar, and they are the primary used in hydraulic systems with pressures over 150 bar. In general, ball valves up to nominal size DN100 are the optimum choice both technically and economically. Larger sizes add significantly to the weight and necessitate a specific turning mechanism, making such valves less appealing.
Gate Valves
Gate valve is one of the most common valves used in ship engines. One of the primary reasons behind it is that they are the most straightforward choice in terms of functionality and design. As the name suggests, the gate valves consist of a gate or the valve disc. This disc performs the vital function of regulating the flow of the liquid that passes through.
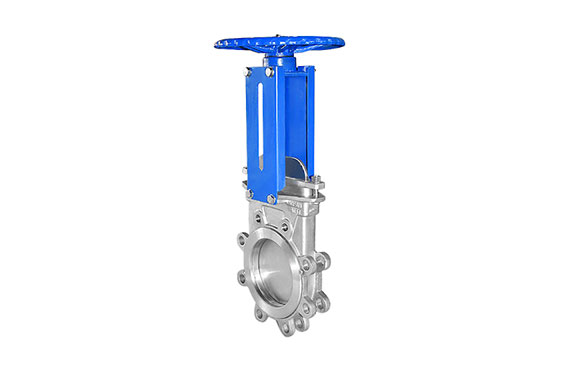
It is worth noting that while using a gate valve, the flow is obtained in two modes, either full-flow or no-flow. That said, there is no in-between. The valves cannot control the flow of the fluid. Instead, it stops the flow completely. Hence, these valves can only be operated in one position. It gives the flow of full bore without changing the direction.
These valves are not suited for operations that require the flow to be partially open. Since it has only two modes, its working is quite simple and doesn’t have any complex mechanisms involved.
The spindle wheel is attached to the spindle rod, which rotates to move the gate at a right angle to the flow of the liquid. There is a screw spindle that works in a nut. The valve is lifted with its help to close or open the gate. The seats and the valves are tapered or parallel on their facing sides.
What is a Ship Engine Room?
The propulsion machinery rooms on a ship are known as the engine room or ER. The equipment required for operations may be divided into several compartments to improve a vessel’s safety and damage resistance. One of these areas is the engine room, which is often the mechanical space’s largest physical compartment.
The vessel’s main propulsion system is kept in the engine room and often includes a diesel engine, gas turbine, or steam turbine. The machinery space on certain ships might include more than one engine room, such as front and aft, port or starboard engine rooms, or it might only be numbered. The engine room is typically small and near the bottom of the vessel’s aft end, where it may be found on the majority of ships and vessels.
More About Ship Engine Rooms
The ship’s engine room houses a range of equipment and mechanisms that cooperate to move the ship from one port to another. Depending on the size and role of the ship, an engine room may be more than one. The rooms can be identified by their locations on the ship, but more often than not, they are numbered to make them stand out from one another. Because there is less space between the engine parts and the propeller that propels the ship forward when there is only one engine room on board, it is most likely to be situated near the back of the ship. A longer propeller shaft is more likely to sustain damage or fail than a shorter one.
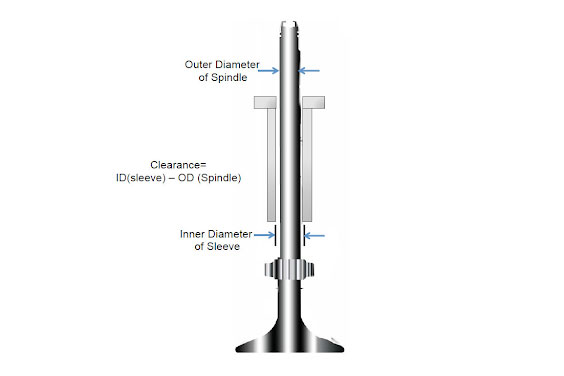
Engine Room Flooding
As evident from the name, engine room flooding indicates filling the engine room with water. Engine room flooding can impact the strong integrity of the ship. The engine room lies at the bottom part of the ship, and in the case of a VLCC or ULCC ship, the platform at the bottom is around 10-15 meters below the water line.
Unsurprisingly, the engine room is filled with pipes and exposed to risky conditions and several hazards. Besides, the main seawater line almost covers the entire engine room, and this pipe has a huge diameter. Therefore any damage in the ship’s engine room can shake the ship’s integrity.
Mentioned below are some reasons why engine room flooding occurs.
1) E.R. or Engine room flooding can occur because of leakage in the E.R. space from the sea, machinery, or freshwater systems. Generally, leakages could be from fresh or sea water coolers, big sea water pumps, boiler water systems, etc.
2) One must identify the leakage when the valve isn’t holding. It could be from the flange joint or identify the leak if the valve is not holding. Once the leak has been identified, repair the leak.
3) Whenever one finds any leak, one must immediately call for help from the coastal state. The ship’s stability will be affected greatly if the leakage isn’t treated properly. In such a situation, the leakage should be stopped or minimized. If the leak happens due to an accident such as grounding or collision, there isn’t much left that could save the ship because the bulkhead opening is large, and thus nothing can save the ship.
4) When a seawater pipe leak is left unattended, it forms a large rupture that causes a sudden inflow of seawater in the engine room.
5) When overboard valves are in a rusted condition, they can cause a rupture of the pipe.
When sea suction filters aren’t boxed adequately. Opening the valve after not tightening it properly can lift the top cover away, thereby making the sea water gush in the engine room.
6) If the boiler blow-down valve is badly rusted or in a very bad condition, it might lead to pipeline rupture, which causes the engine room to flood with seawater and boiler water.
Engine Room Flooding Common Reasons
There are primarily three causes of engine room flooding:
- Equipment And System Leaks
Engine room flooding may occur due to leaks from machinery, freshwater, seawater system, or engine room space itself. Leaks typically come from large seawater pumps, seawater or freshwater coolers, boiler feed water systems, etc.
2. If The Overboard Valve Were To Leak
If the leak originates from the valve and the valve is holding it closed, the system that controls it allows the ship to function normally even when it is closed. Find the leak if the valve is not holding. Try to fix the leak; it can come from the flange joint or valve stem gland.
3.Flooding Brought On By A Hull Break Or Tiny Hole
In this situation, call the nearest coastal state for assistance as soon as you discover the leak since if it spreads further, the ship’s stability would be compromised. The leaking must be reduced to a minimum and ultimately halted.
Actions To Be Taken During ER Flooding
Below are a few everyday actions you should take during E.R. floods to prevent them or ensure there is no significant damage.
- The sooner you find the fault in the engine, the better it will be to handle the situation.
- If the flood has already happened, the situation needs to be tackled. Hence, you should call for the maximum workforce to handle the situation.
- Then and there, inform the chief engineer about the situation and follow the instructions.
- The inlet and the outlet valves of the impacted system should be closed to stop the leak.
- Remember not to use the tank until the welding or cement boxing is done.
- When there is a leakage, you should start transferring the extra content from the leaking tank to another tank and try to minimize the leak to the extent possible.
When there are leaks because of the overboard valve:
- You will have to identify the leak if there is no holding valve. It can be from the flange joint or the valve stem gland, and try to repair the leak if that is possible.
- If you have added a temporary fix after the ship has reached the port, call for the divers. They will help the valve open from the outside and find a permanent repair.
- Suppose the system for the valve can be isolated without causing any disruption to the normal operations of the ship. Putting a plank in the valve may also help in achieving better results.
Flooding results from a small hole in the hull or some crack in the hull.
- No matter what means you try, the leakage must be minimized or stopped to prevent further damage.
- When this situation occurs, you should get the leak traced as soon as possible by seeking help from the nearest coastal state. This is vital because if the leak is a major one, the stability of the leak will be affected.
- In case of the announcement of an abandoned ship signal, the crew will have to muster to their specific lifeboats, and the abandon ship operations should be carried out.
- If the leak is the result of an accident or damage of any kind, like grounding or collision, you will not be able to do much because there is a large opening at the bulkhead, and the leak can’t be stopped. During such cases, the captain is responsible for deciding whether the ship will be a safe place to stay or the ship has to be abandoned.
Engine Room Flooding
There can be incidents when the engine room flooding occurs because of the preparation for cleaning the filter of the seawater inlet. The cleats on the filter were released, and soon when it was done, the seawater flooded the engine room. After forty minutes, when the filter was opened, the steering gear compartment and engine room flooded.
If you think about it, there can be some underlying causes that resulted in the incident. Some of them were inadequate procedures, improper planning, and also lack of adherence to the correct set of procedures.
This incident will lead to learning a few lessons.
- All remotely operated valves should be secured against all unintentional operations. This should be done before getting started with the removal of the filter cover.
- The position of the valve on both sides of the seawater inlet filter is a critical consideration. You should ensure all the valves are closed even before the filter is opened. If there is an interruption, the position of the valves should be re-checked before the commencement of the work.
- The process of re-tightening or removal of the filter cover is essential. If you remove the cleats from the hinges cover in a random sequence, there can be a loss of the re-tightening possibility of the cover. The cleats should be kept in place until it is entirely safe to remove the cover. While tightening the cleats, the same procedures should be followed to avoid the situation of incorrect tightening of the cover.
- All risks of errors and misunderstandings will be significantly reduced if the same person carries out the entire cleaning procedure. This will also help avoid all kinds of interruptions during work.
- After tightening the cleats and cleaning the filter, you should open the valves carefully on each side and check for normal operations.
How To Avoid E.R. Flooding?
The “Emergency Bilge Suction Valve” is the primary safety feature offered to prevent engine room flooding. This valve is identical to a standard globe valve; however, it is typically of the “screw-down non-return” kind. This valve can be operated in two or three positions and is situated on the platform’s bottom edge.
The valve is linked to a conduit that is left open in the engine room bilge so it can accept suction. The suction side of the engine room’s largest capacity pump, the seawater pump, is connected to the valve’s other end. The valve may also be connected to the ballast pump if it is the engine room pump with the maximum capacity.
Engine Room Flooding Procedures
As discussed, there are several ways in which a ship’s engine room gets flooded. The ship floats on seawater, so the risk of flooding is always there. To control the situation or prevent flooding, a few things must be taken care of. The level of the incoming seawater in the bilges should be controlled so that the water doesn’t reach the main power generator.
The situation can be catastrophic where the main power to the engine and the pump get lost. One can prevent this by opening the bilge suctions and activating the bilge pump. That said, even after trying all these things, if the water level isn’t controlled, then one should operate an emergency bilge injection valve for the best results.
Safety Arrangements
The major safety arrangement provided to prevent or tackle engine room flooding is making provision for an “Emergency Bilge Suction Valve.” This valve is the same as the normal globe valve. There is a specific “screw-down non-return” type. The valve is usually located at the bottom and several locations from where the valve is being operated. The engine room flooding in the ship is an emergency situation, and adequate steps should be taken to ensure that there is no major destruction in the ship.
Operating The Emergency Bilge Injection Valve
As the name suggests, this injection valve should only be employed in emergencies. That said, the use of this valve is only recommended at the time of engine room flooding. The valves are connected to the pumps with maximum lift capacity.
- The suction pipe is fitted on the tank top and below the valve. It will not be found above the bilge well. The reason behind this is that the risk of choking increases during operation.
- The hand wheel operating the valve is painted in red color. The spindle gets extended below the engine room plates to the valve manifolds. The main suction valve of the seawater is contained in it from the sea chest and the emergency bilge injection valve. This emergency injection valve is also the Screw Down Non-Return Valve (S.D.N.R.V.).
- The operations of the valve should be noted and checked at regular intervals to ensure that the handwheel is flexible enough. Also, it should be operated freely using hands. That said, the user shouldn’t have to use a spanner or a wheel key to spin the wheel.
- If the situation is normal and manageable, bilge water will quickly pass through the oil water separator before being discharged overboard. One should directly pump the water discharged from the engine room when it gets flooded overboard. One should inform the port authorities about the situation as well.
Daily Maintenance Of Ship E.R.
Any mechanical device or piece of machinery must undergo maintenance to be operational. Effective maintenance can contribute to a structure’s extended life and beneficial results, whether a tiny piece of equipment or a huge one. One way to keep equipment on a ship up to date and in good working order is through maintenance.
Engineers and crew do the necessary maintenance for a ship’s safe and effective functioning in the engine room, which houses most of the equipment. Every piece of equipment on board a ship needs regular maintenance, which must be done.
Early ships had a huge crew and number of engineers, making maintenance quick and simple. However, the ship’s crew and engineering staff have dramatically decreased under the current situation.
Whenever there is a flood in the ship’s engine room, an emergency should be announced, and everyone on the ship should be made aware of the case so that the required actions are taken as fast as possible. Also, it is important to reach out to the repair team of professionals at the earliest. The consequences of getting water filled can be many, so you must ensure all leaking pumps, pipes, coolers, etc. You should make sure that there is effective damage control and also ensure adequate stability.
Conclusion
Engine room flooding is not an easily manageable situation. It leads to numerous problems and needs to be resolved at the earliest. Many tasks need to be carried out in the backend to ensure no significant destruction because of the flood. Also, people need to be aware of what not to do in such a situation as the situation might go out of hand anytime.
There are several reasons behind the unwanted ingress of seawater. Also, one should handle the situation mindfully and take steps to avoid significant damage. For purchasing high-quality and reliable valves from a reliable supplier, please reach out to us.